Magnesium phosphate cement (MPC) has the characteristics of negative temperature curing, fast setting and hardening, high strength, strong bonding ability, low shrinkage rate and biological activity. It has attracted widespread attention in the fields of rapid/emergency repair of existing structures, nuclear waste and heavy metal solidification, bone repair and 3D printing.
Low-activity magnesium oxide is the key raw material for preparing MPC. The low-activity magnesia for preparing MPC is mainly dead burnt magnesia sintered at 1500~1800℃ for 5~10h. The current process for producing dead burnt magnesia has high energy consumption and low equipment turnover efficiency, resulting in high energy consumption and high cost for preparing MPC. Moreover, the acid-base reaction rate between the commercially available dead burnt magnesia and the phosphate solution is relatively fast. When preparing MPC, it is necessary to add a B-containing retarder to slow down the solidification rate of the slurry in order to obtain sufficient operating time. But on the one hand, the B-containing retarder reduces the early performance of MPC, on the other hand, the B-containing retarder is expensive, which further increases the cost of MPC, which is not conducive to popularization and application.
In response to this scientific problem, the team of associate researcher Li Ying from ISL prepared low-activity magnesium oxide by calcining light burnt magnesia powder and brucite at ≤1200℃, using common elements such as B, Na, K and Cl's sintering effect. The experiment measured the physical characteristics of low-activity magnesium oxide such as particle size, specific surface area, porosity, chemical composition, mineral composition and morphology, as well as the setting time, hydration products, microstructure, and compressive strength of MPC prepared by low-activity magnesium oxide , volume stability and other setting and hardening properties, and analyzed the effect of sintering temperature on the physical and chemical properties of low-activity magnesium oxide and the setting and hardening properties of MPC. Compared with the prior art, the sintering effect of salt lake co-existing elements can reduce the sintering temperature of magnesium oxide from 1500 to 1800°C to below 1200°C, which is conducive to the realization of low energy consumption and low-cost green preparation of low-activity magnesium oxide and MPC. Promote the promotion and application of MPC. For details, please see "Research Highlights" in the second issue of chemistry special issue of "Salt Lake Research" in 2020: 15-25.
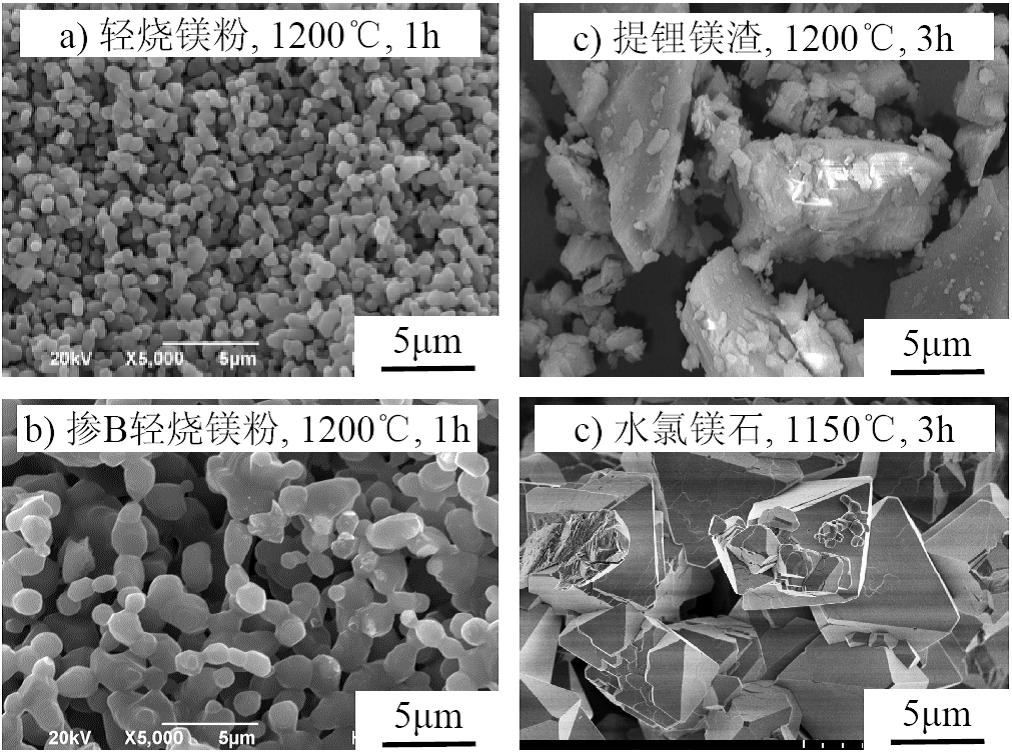
Morphology of sintered magnesia
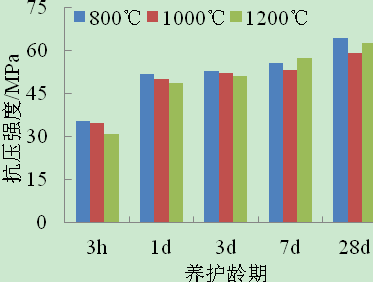
Compressive strength of MPC prepared by sintering magnesium oxide